Mi sono mai chiesto cosa succede a rendere quei pennelli per il trucco impeccabili che ti aiutano a raggiungere il tuo look perfetto? Come produttore di pennelli estetici, Sappiamo esattamente come creare i tuoi pennelli per il trucco, Ed è un processo affascinante. Dalla selezione di materiali di alta qualità alla messa a punto ogni pennello, Ogni passo è cruciale per la consegna di un prodotto che si distingue. Siamo entusiasti di condividere con te il nostro processo di fabbrica in 12 passaggi, dandoti uno sguardo dietro le quinte a come portiamo i nostri pennelli dal concetto alla realtà.
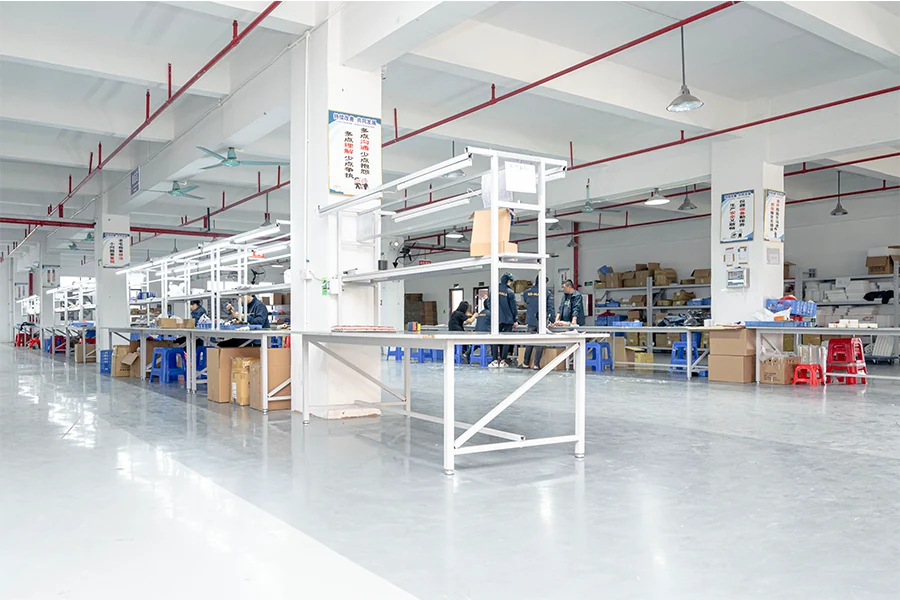
12 Passaggi per produrre in serie spazzole estetiche
Come produttore di pennelli per trucco personalizzati e fornitore di spazzole cosmetiche OEM, Seguiamo meticolosamente un 12-Processo di passaggio Per garantire che ogni pennello soddisfi i più alti standard di qualità, prestazione, e durata. Ecco come lo facciamo:
Fare un passo 1: Pesare
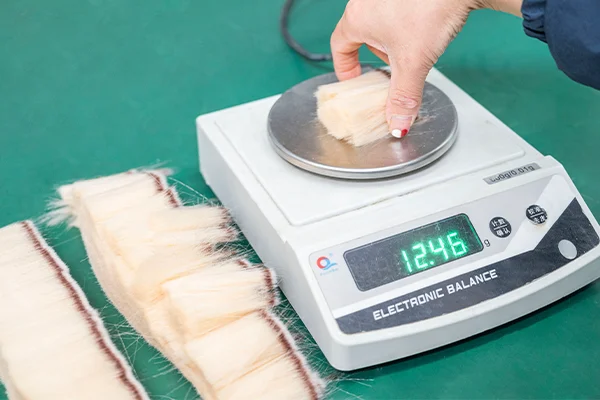
La base della produzione di spazzole per il trucco di alta qualità risiede nella precisione del processo di pesatura. La pesatura non significa solo misurare le setole, ghiere, e maniglie: si tratta di garantire coerenza tra migliaia di pennelli. Anche una piccola deviazione di peso può portare a incoerenze nel prodotto finale, influenzando l'equilibrio e le prestazioni.
Ad esempio, Il peso delle setole naturali può variare leggermente a causa del contenuto di umidità, Quindi condizioniamo le setole in un ambiente controllato con scale avanzate e sistemi computerizzati prima di pesarli. Questo passaggio è spesso trascurato, Ma è essenziale raggiungere un aspetto uniforme e una funzionalità attraverso un lotto.
Fare un passo 2: Carta
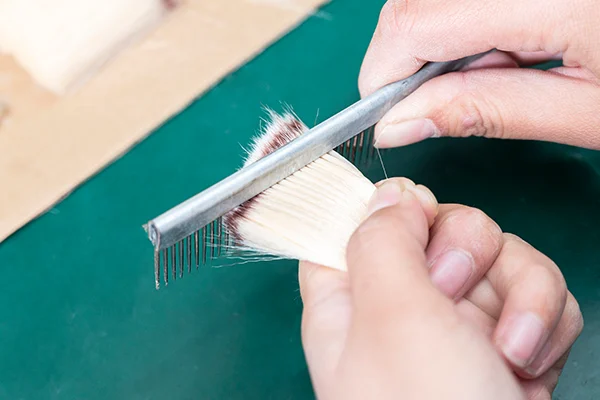
La carding è un processo delicato che richiede l'attrezzatura giusta e una comprensione del tipo specifico di setole utilizzate. Sia lavorare con fibre sintetiche o naturali, Il processo di carding deve essere regolato per soddisfare le loro caratteristiche uniche.
Per esempio, Le setole naturali tendono ad avere lievi variazioni di spessore e consistenza, Quindi utilizziamo le impostazioni personalizzate sulle nostre macchine per cardare per separare delicatamente e allineare queste setole senza danneggiarle. Questa attenzione ai dettagli assicura che le setole siano perfettamente allineate senza grovigli.
Fare un passo 3: Tocca in tazza
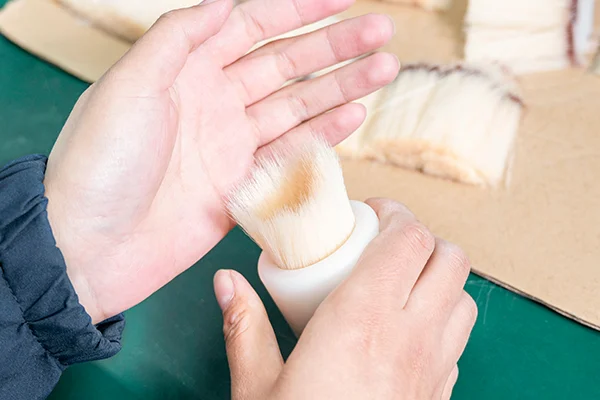
Toccare in una tazza potrebbe sembrare semplice, Ma è un passo in cui la precisione è la chiave. Quando le setole vengono posizionate nel dispositivo a forma di coppa, L'obiettivo è creare una distribuzione uniforme senza causare alcun disallineamento. Una svista comune non è in grado di spiegare la conicità naturale delle setole, che può portare a una forma irregolare se non correttamente gestita.
Ci rivolgiamo a questo utilizzando apparecchi personalizzati su misura per il tipo di pennello specifico per garantire che le setole siano uniformemente sfruttate in posizione e preservino il cono naturale mentre si formano la forma desiderata del pennello.
Fare un passo 4: Stringere con il filo
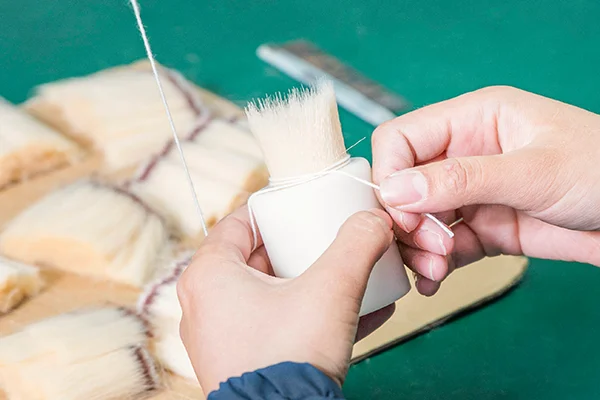
Il prossimo passo è il serraggio con il filo, dove un filo fine è avvolto attorno alla base delle setole per fissarle in posizione. La tensione del thread deve essere attentamente controllata, troote, e le setole potrebbero essere danneggiate; Troppo sciolto, E non saranno sicuri.
Utilizziamo thread specializzati progettati per espandersi leggermente quando esposti all'adesivo, Garantire un stretto, Fit sicuro senza compromettere l'integrità delle setole. Inoltre, Ispezioniamo meticolosamente il processo di threading per garantire che nessuna setola sia pizzicata o fuori luogo, che potrebbe influenzare le prestazioni e la durata del pennello.
Fare un passo 5: Rotolo & Massaggio
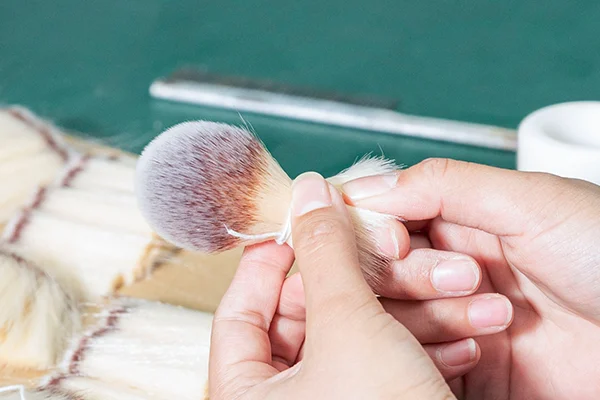
Rotolare e massaggiare le setole migliorano la loro flessibilità e morbidezza. Questo passaggio è particolarmente importante per i pennelli destinati a applicazioni delicate, come la miscelazione o l'applicazione di polveri. Una svista comune è trascurare l'impatto della direzione e della pressione di rotolamento sulla trama finale delle setole.
Utilizziamo rulli personalizzati con impostazioni regolabili che ci consentono di controllare la quantità di pressione e la direzione del rotolamento, Garantire che ogni pennello raggiunga il perfetto equilibrio di morbidezza e resilienza. Questo passaggio non solo migliora la sensazione del pennello, ma anche la sua capacità di raccogliere e distribuire uniformemente il trucco.
Fare un passo 6: Taglia i suggerimenti
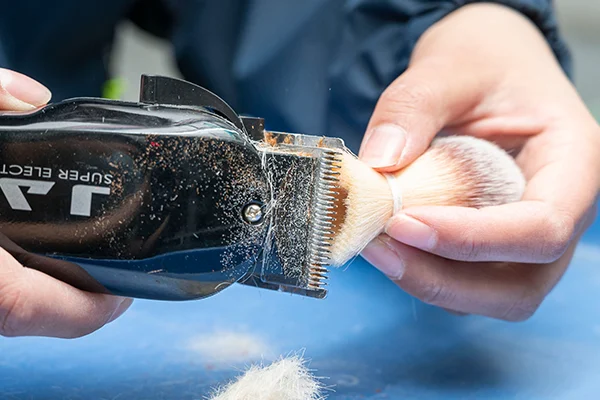
Tagliare le punte delle setole è dove il pennello inizia ad assumere la sua forma finale. La precisione è fondamentale qui, Mentre il taglio determina come il pennello interagirà con la pelle. Utilizziamo utensili da taglio ad alta precisione calibrati a tolleranze micrometriche, Garantire che ogni setole sia tagliata alla lunghezza e all'angolo esatto richiesto.
Un dettaglio che viene spesso trascurato è la necessità di smussare leggermente le punte delle setole per alcuni tipi di pennello, come quelli usati per la miscelazione. Questa sottile modifica migliora la capacità del pennello di creare liscio, transizioni senza soluzione di continuità nelle applicazioni di trucco, Una funzionalità che gli utenti apprezzeranno.
Fare un passo 7: Installare nella ghiera
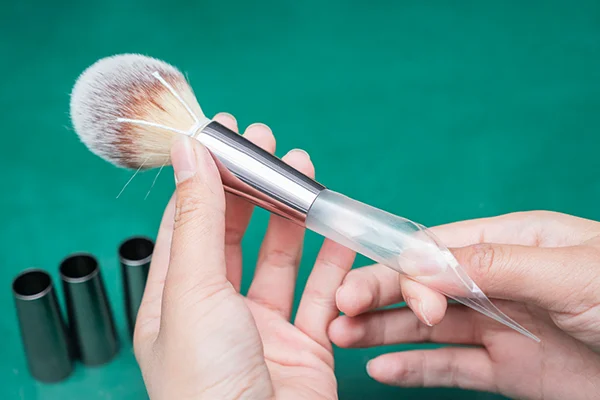
Qualsiasi disallineamento può influenzare le prestazioni e la longevità del pennello. Utilizziamo ferruli progettati personalizzati su misura per il tipo di pennello specifico, Garantire una vestibilità comoda che tiene saldamente le setole. Inoltre, Pretrarviamo l'interno della gernella con un agente di legame per migliorare l'adesione tra le setole e la ghiera. Questo passaggio è spesso trascurato ma è essenziale per prevenire lo spargimento di setole e mantenere l'integrità strutturale del pennello nel tempo.
Fare un passo 8: Premere la galleria
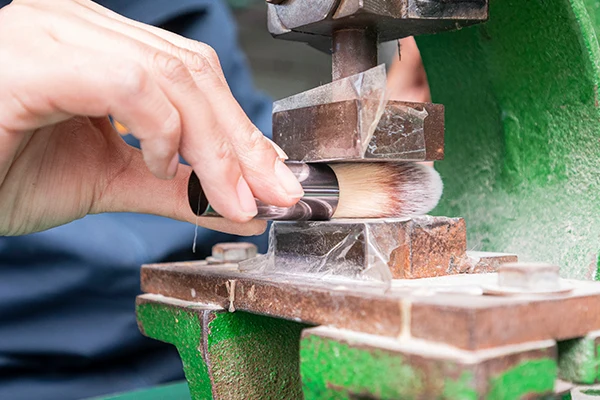
Una volta installate le setole, Procediamo a premere la galleria per assicurarla saldamente in atto. Usiamo presse idrauliche con impostazioni di pressione regolabili, permettendoci di personalizzare la forza di pressione sul tipo di pennello specifico. Per garantire che il trattore sia premuto uniformemente, Utilizziamo maschere personalizzate che allineano perfettamente la galleria prima di premere. Ciò garantisce un legame uniforme tra le setole e il Ferrule, che è fondamentale per la durata e le prestazioni del pennello.
Fare un passo 9: Riempire la colla
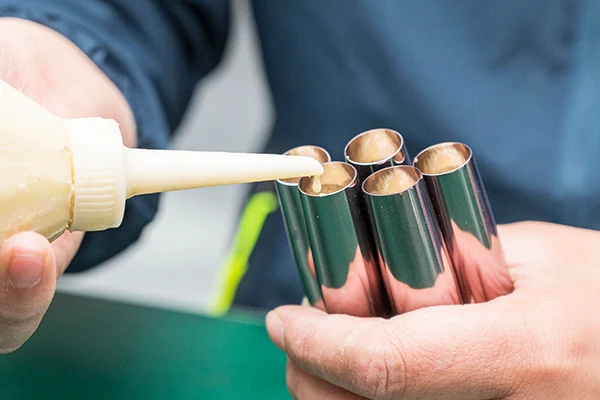
Il tipo di colla utilizzata è importante quanto la quantità applicata. Usiamo adesivi ad alte prestazioni che sono specificamente formulati per i pennelli cosmetici, e progettato per resistere all'uso ripetuto e all'esposizione ai prodotti per il trucco. La colla viene applicata utilizzando distributori di precisione che controllano la portata, Garantire una distribuzione uniforme in tutto il Ferrule. Usiamo anche un processo assistito dal vuoto per rimuovere eventuali bolle d'aria dalla colla, che può compromettere la forza del legame. Questo livello di dettaglio garantisce un legame durevole che mantiene le setole saldamente in atto per la vita del pennello.
Fare un passo 10: Cottura al forno & Forma

Cuocere e modellare è un processo che solidifica il legame tra le setole e il Ferrule, pur finalizzando anche la forma del pennello. Deve essere attentamente controllato per evitare il surriscaldamento, che può danneggiare le setole o indebolire la colla. Usiamo forni con un controllo preciso della temperatura, Garantire che la colla si curerà correttamente senza influire sulle setole’ integrità.
Anche modellare il pennello durante questa fase è cruciale, mentre imposta la forma finale delle setole. Utilizziamo stampi personalizzati progettati per ottenere la forma esatta richiesta per ciascun tipo di pennello, Garantire coerenza attraverso grandi corse di produzione.
Fare un passo 11: Ordinare
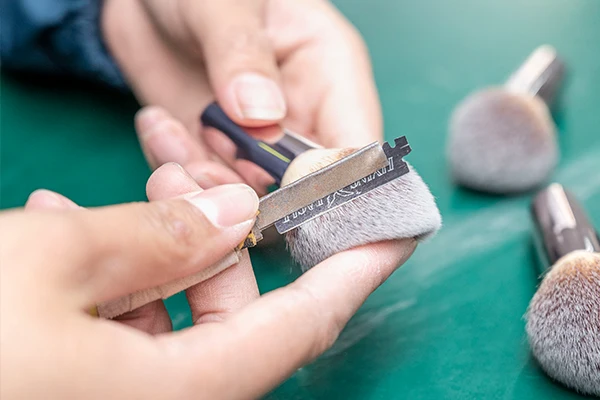
Il taglio è l'ultimo passo per perfezionare la forma e la lunghezza delle setole. Usiamo macchine di taglio avanzate dotate di sensori ad alta risoluzione che rilevano e si adattano anche alle minime variazioni della lunghezza delle setole. Questo passaggio è particolarmente importante per i pennelli speciali, come disegni angolati o affusolati, dove anche le deviazioni minori possono influire sulle prestazioni del pennello. Dopo il taglio, Ogni pennello subisce un'ispezione approfondita per garantire che soddisfi i nostri rigorosi standard di qualità.
Fare un passo 12: Collegare la maniglia
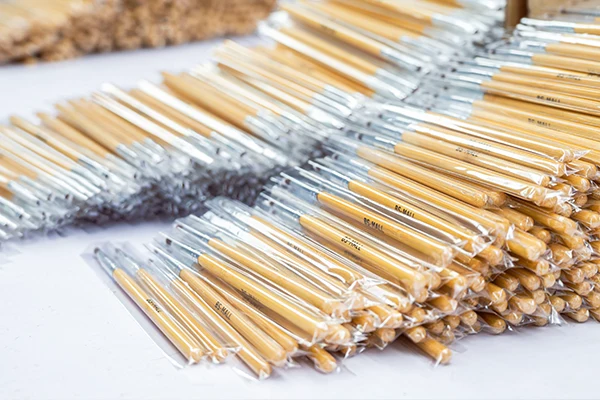
Il passaggio finale nel processo di produzione è collegare la maniglia alla ghiera, e completando l'assemblaggio del pennello. Il processo di attacco della maniglia è più complesso di quanto potrebbe apparire. Utilizziamo maniglie progettate su misura che sono accuratamente abbinate alla ghiera, Garantire una vestibilità sicura e confortevole.
Il processo di connessione prevede non solo la protezione della maniglia con adesivo, ma anche l'uso di strumenti di allineamento di precisione per garantire che il pennello sia perfettamente bilanciato. Un pennello ben bilanciato è più facile da controllare e offre un'esperienza utente più confortevole, Ecco perché ci prendiamo cura di più in questa fase di assemblaggio finale.
Servizi a valore aggiunto opzionale
Oltre al nostro meticoloso processo di produzione, Offriamo una gamma di servizi a valore aggiunto opzionali progettati per migliorare il tuo marchio e le offerte di prodotti. Questi servizi ti consentono di differenziare i tuoi prodotti e fornire valore aggiunto ai tuoi clienti, Garantire che i tuoi pennelli si distinguano nel mercato competitivo. Ecco come possiamo supportarti:
Progettazione di brevetti
Come produttore di pennelli estetici OEM lungimirante, Comprendiamo l'importanza di proteggere i tuoi design unici. Offriamo servizi completi di progettazione di brevetti per garantire il tuo Pennici per il trucco personalizzate sono salvaguardati contro l'imitazione. Il nostro team lavora a stretto contatto con te per sviluppare progetti di pennelli innovativi che non solo si distinguono sul mercato, ma mantengano anche la protezione legale di cui hai bisogno per preservare l'integrità del tuo marchio.
Marchio ed etichettatura
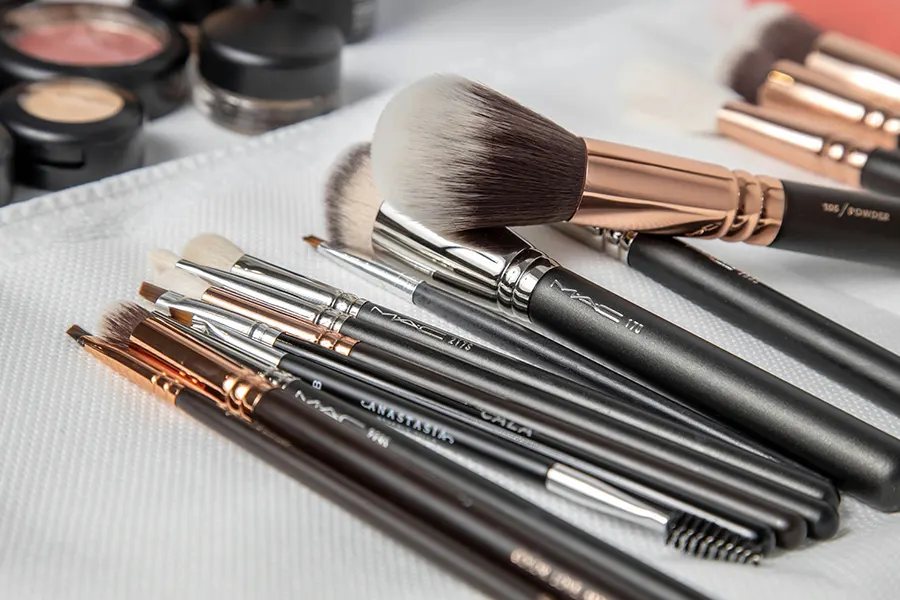
Il branding e l'etichettatura sono elementi fondamentali per stabilire la tua presenza nel settore della bellezza competitiva. Come a produttore di spazzole per il trucco a margine di etichetta, Offriamo soluzioni di branding personalizzate, Compreso il posizionamento del logo, schemi di colore, ed etichettatura unica, per allineare con l'identità del tuo marchio. Le nostre tecniche di stampa avanzate assicurano che il logo e i dettagli del tuo marchio siano visualizzati con chiarezza e durata, Aiutare i tuoi pennelli a fare un'impressione duratura sui clienti.
Imballaggio personalizzato
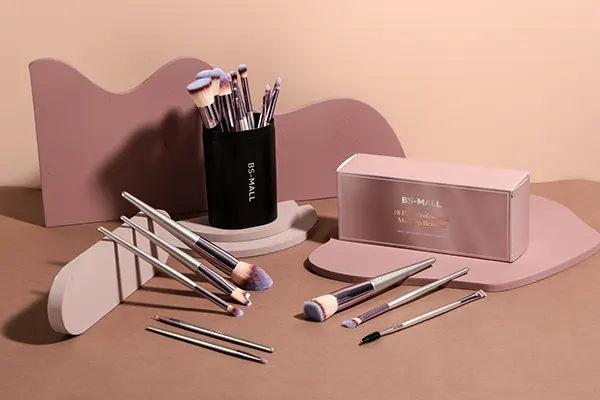
Per i migliori marchi di spazzole per trucco di qualità, L'imballaggio è importante quanto il prodotto stesso. Offriamo design su misura per interni ed esterni. Se hai bisogno di elegante, imballaggio moderno o qualcosa di più lussuoso, Possiamo creare design che riflettano l'immagine del tuo marchio e appello al tuo pubblico di destinazione. I nostri servizi di imballaggio personalizzati assicurano che ogni aspetto del tuo prodotto, Dal primo sguardo all'esperienza di unboxing, comunica la qualità e la raffinatezza.
Kit campione gratuito
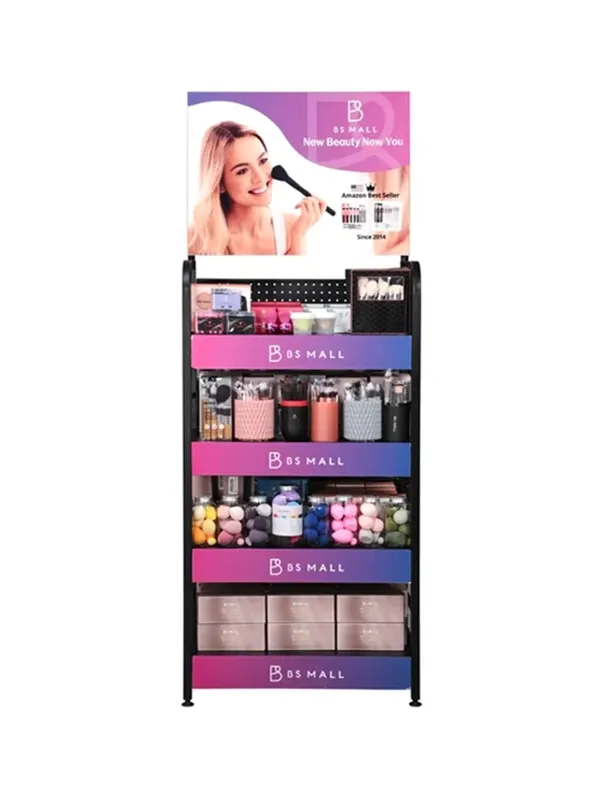
Per aiutarti a prendere decisioni informate, Forniamo kit campione gratuiti valutati a over $5,000. Questi kit includono una varietà dei nostri pennelli di alta qualità, Mostrare progetti e materiali diversi, Quindi puoi sperimentare la nostra artigianato in prima persona. Offriamo anche quantità minime basse, a partire da giusto 50 pezzi, rendendo più facile iniziare in piccolo e aumentare secondo necessità. Inoltre, Forniamo immagini di alta qualità e copia per scopi promozionali, permettendoti di commercializzare i tuoi pennelli in modo efficace dall'inizio.
Conclusione
Comprendere come creare i tuoi pennelli per il trucco può trasformare il tuo approccio al settore della bellezza. Come fornitore di fiducia, Crediamo nella condivisione della nostra esperienza per aiutarti a vedere il processo meticoloso dietro ogni pennello. Padroneggiando questi passaggi, Ti assicurerai che i tuoi pennelli non siano solo di alta qualità, ma anche su misura per le tue esigenze specifiche. Siamo qui per supportarti ogni passo, Fornire le conoscenze e gli strumenti per elevare le offerte dei prodotti e soddisfare le tue esigenze di mercato con fiducia.